MyPlasm CNC machines are popular among hobbyists and professionals alike. While they have a lot to offer in terms of power, precision, and versatility, they’re not without their quirks.
In this article, we’ll dive deep into some of the most common problems with MyPlasm CNC machines and offer solutions to help you get the most out of your plasma-cutting experience.
MyPlasm Cutter Not Working: A Troubleshooting Guide
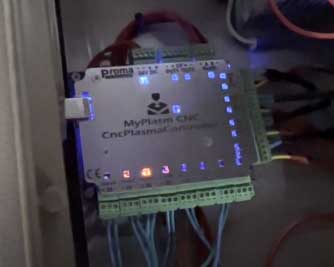
One of the most frustrating issues MyPlasm users encounter is when the cutter suddenly stops working.
Before you start tearing your hair out, let’s look at some potential reasons why this might be happening:
- Power Supply Issues
This is perhaps the most obvious reason your MyPlasm cutter might not be working.
Double-check your power supply connections and ensure your machine is receiving adequate voltage.
If the voltage is too low, your cutter won’t have the power it needs to operate effectively.
- Faulty Connections or Damaged Cables
Inspect your connections and cables for any visible damage. Loose or damaged connections can result in power loss, which can cause your MyPlasm cutter to stop working altogether.
- Worn or Damaged Consumables
Plasma consumables, such as the nozzle and electrode, wear out over time. If they’re damaged or too worn, they can cause your cutter to stop working. Regularly inspect and replace your consumables to ensure optimal performance.
MyPlasm Cutter Keeps Cutting Out: Possible Causes
If your MyPlasm cutter keeps cutting out during use, it could be due to several reasons:
- Overheating
Overheating is a common issue with plasma cutters, and it can cause your machine to cut out abruptly. Make sure your cutter is well-ventilated, and avoid using it for extended periods without breaks to prevent overheating.
- Air Pressure Problems
Air pressure is essential for plasma cutting, and insufficient pressure can cause your cutter to cut out. Ensure that your air compressor is working correctly and that there are no leaks or obstructions in your air supply system.
- Incorrect Settings
Using the wrong settings for your specific cutting task can cause your MyPlasm cutter to cut out. Double-check your settings, such as amperage, air pressure, and cutting speed, to ensure they’re appropriate for the material and thickness you’re cutting.
How To Identify Bad Plasma Consumables?
Plasma consumables wear out over time, and using bad consumables can lead to poor cutting quality or even damage to your cutter. Here’s how to spot bad consumables:
- Inspect the nozzle and electrode for visible damage, such as cracks, burn marks, or excessive wear.
- Pay attention to your cutting quality. If your cuts are becoming less precise or clean, it could be a sign that your consumables need to be replaced.
- Monitor your cutting speed. If you notice a sudden drop in speed, your consumables might be worn out.
Common Issues When Plasma Cutting
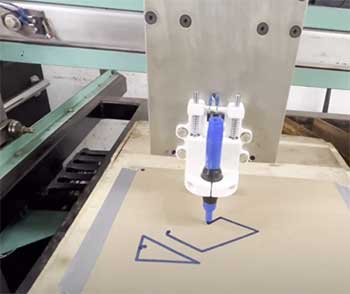
Plasma cutting is a powerful and versatile tool, but it’s not without its challenges.
Some common issues you might encounter include:
- Dross formation: This is the accumulation of molten material on the edges of your cuts. It can be caused by incorrect cutting speed, incorrect amperage, or using worn-out consumables.
- Warping: This occurs when the heat from the plasma cutter causes the material to distort. To minimize warping, use a lower amperage, ensure proper clamping, and make multiple passes if needed.
- Incomplete cuts: This can happen if the cutting speed is too high or if the consumables are worn out. Adjust your cutting speed and replace consumables as needed to ensure clean, complete cuts.
- Poor cut quality: This issue can arise from a variety of factors, such as using incorrect settings, using bad consumables, or having an unstable workpiece. To improve cut quality, double-check your settings, replace consumables when necessary, and ensure your workpiece is secure.
Cutting Rusty Metal With A Plasma Cutter: Is It Possible?
Yes, you can use a plasma cutter on rusty metal, but it’s essential to consider a few factors to ensure a successful cut. Here are some tips for cutting rusty metal with your MyPlasm CNC machine:
- Use a higher amperage: Rusty metal can be more challenging to cut than clean material, so you may need to increase your amperage to achieve a clean cut.
- Adjust your cutting speed: Cutting rusty metal may require a slower cutting speed to ensure the plasma arc can penetrate the rust and make a clean cut.
- Clean the metal surface: While it’s possible to cut through rust, removing as much rust as possible before cutting will improve cut quality and prolong the life of your consumables.
Also Read: All You Need To Know About QueenBee PRO CNC.
Frequently Asked Questions (FAQ)
Your MyPlasm cutter might not be working due to power supply issues, faulty connections or damaged cables, or worn or damaged consumables. Check your power supply, inspect your connections and cables, and replace any worn consumables to get your cutter back up and running.
Your MyPlasm cutter might keep cutting out due to overheating, air pressure problems, or incorrect settings. Ensure your cutter is well-ventilated, check your air compressor and air supply system, and double-check your settings to prevent your cutter from cutting out.
You can identify bad plasma consumables by inspecting them for visible damage, monitoring your cutting quality, and paying attention to your cutting speed. Replace consumables showing signs of wear or damage to maintain optimal cutting performance.
Common issues when plasma cutting includes dross formation, warping, incomplete cuts, and poor cut quality. To minimize these issues, ensure you’re using the correct settings, replace worn consumables, and secure your workpiece properly.
Yes, you can use a plasma cutter on rusty metal. However, it’s important to use a higher amperage, adjust your cutting speed, and clean the metal surface as much as possible before cutting to ensure the best results and prolong the life of your consumables.
Wrapping Up
In conclusion, while MyPlasm CNC machines offer a powerful and versatile cutting solution, they can sometimes present challenges.
By understanding common problems and how to address them, you’ll be well-equipped to get the most out of your MyPlasm CNC machine and enjoy a smooth, efficient cutting experience.